Shape-Shifting Robots: The Future of Soft Robotics
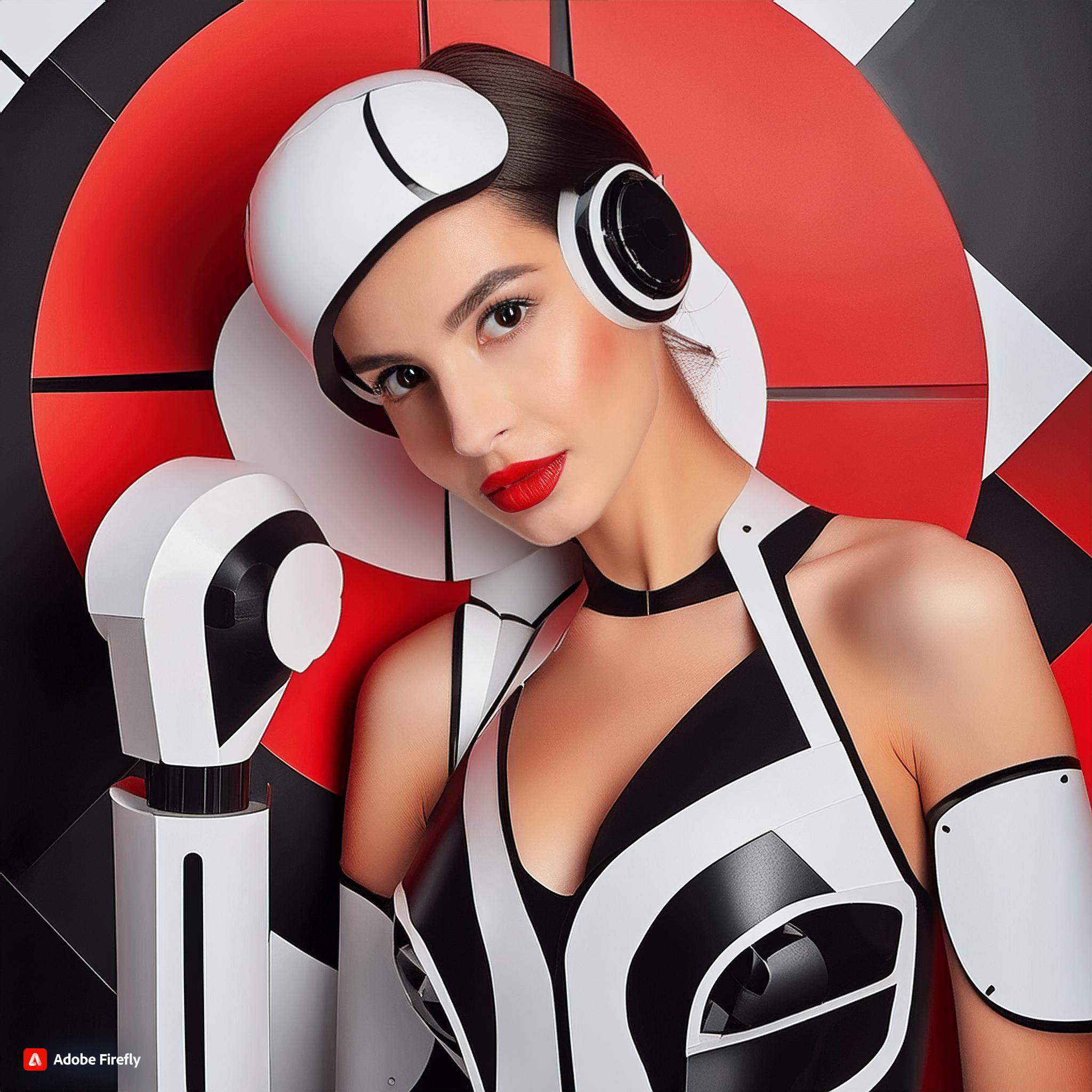
In a groundbreaking development, researchers from The Faboratory at Yale University have created a soft robot capable of detaching and reattaching its limbs, a feature inspired by the natural abilities of lizards and ants. This innovation, described in a recent paper, allows the robot to change its shape on demand, enhancing its adaptability and functionality. This remarkable ability was demonstrated by a hand-sized, three-legged robot that could leave its fourth leg behind and continue moving, mimicking the natural escape mechanisms of certain animals.
The soft robot employs asymmetrically stiff air chambers, which inflate and deflate to generate motion. Its unique joints use a new material called bicontinuous thermoplastic foam (BTF), which supports a sticky polymer. This polymer, solid at room temperature, can melt and reform, enabling the robot to detach and reattach its limbs within about 10 minutes. These joints can withstand several hundred cycles of reattachment and are resilient against dirt and water.
While modular robotics have previously utilized mechanical connections and magnets for similar purposes, these systems are inherently rigid. The innovation at Yale, however, represents the first fully soft reversible joint, paving the way for more flexible and adaptive robotic systems. This advancement highlights the potential for intelligent agents and digital employees that can modify their shape to perform various tasks, increasing their utility in dynamic environments.
This technology, although still in its early stages, opens up numerous possibilities for the future of robotics. As researchers continue to refine these systems, we could see the emergence of non-human workers capable of complex, shape-shifting behaviors, making them indispensable in fields ranging from disaster response to healthcare.
Key Highlights:
- Innovation: Soft robot capable of detaching and reattaching its limbs.
- Inspiration: Mimics natural abilities of lizards and ants.
- Mechanism: Uses asymmetrically stiff air chambers and bicontinuous thermoplastic foam (BTF) for motion and joint functionality.
- Process: Joints melt and reform, enabling limb detachment and reattachment in about 10 minutes.
- Durability: Joints withstand several hundred reattachment cycles and are resilient against dirt and water.
- Advancement: Represents the first fully soft reversible joint, enhancing flexibility and adaptability in robotics.
- Implications: Potential for intelligent agents and digital employees to perform various tasks in dynamic environments.
- Future: Promises advancements in fields such as disaster response and healthcare.
Reference: