Tesla’s Bold Move into the World of Robotics: Optimus Robots to Revolutionize Manufacturing
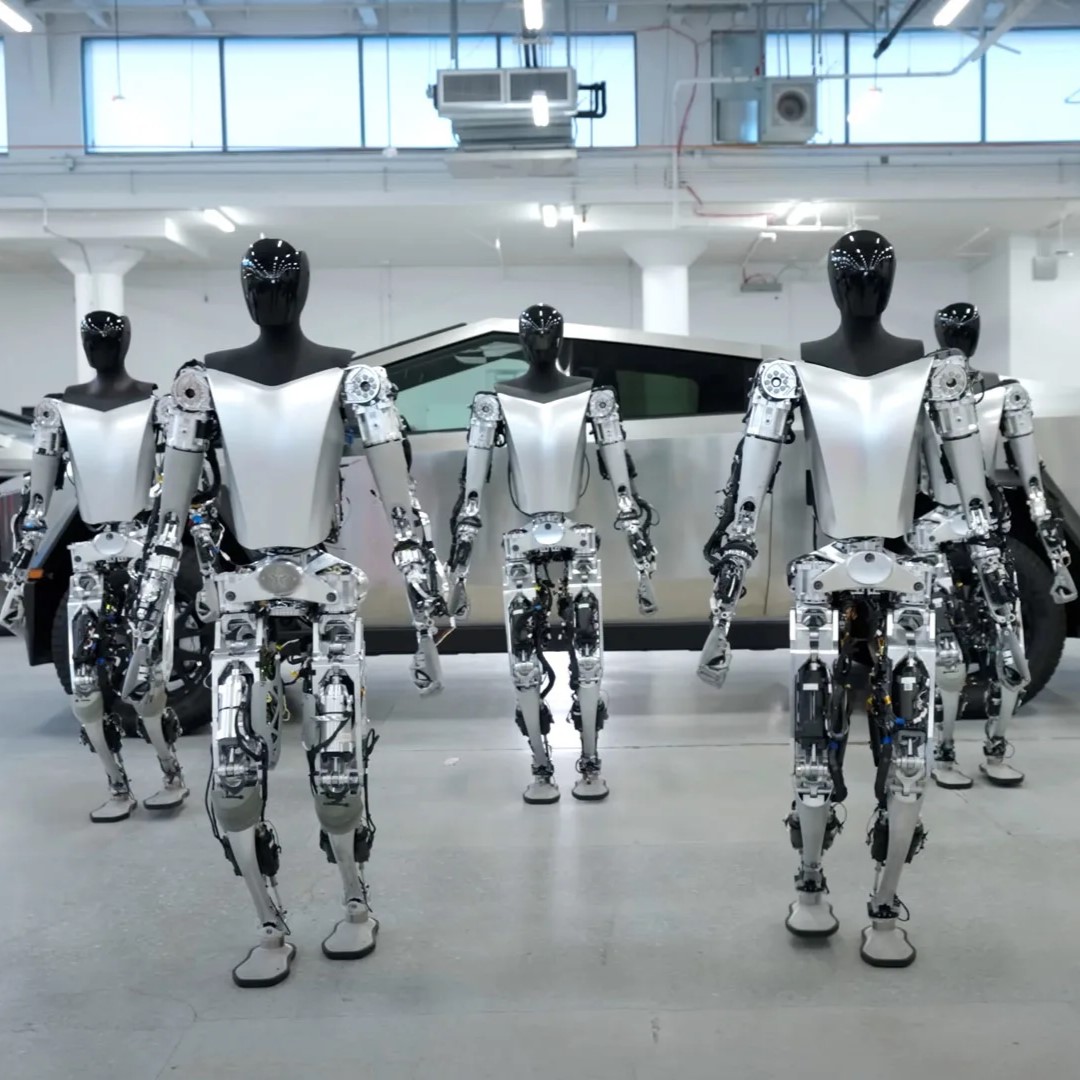
A Vision for the Future of Work
In April 2025, Tesla made waves with an ambitious announcement: the company plans to deploy humanoid robots, named Optimus, in its factories by the end of the year. Tesla CEO Elon Musk believes these robots could be the key to propelling the company's value to an astronomical $25 trillion, more than half the size of the entire S&P 500. The move is part of a broader strategy to integrate Artificial Intelligence (AI) and automation into manufacturing processes, with significant implications for both the workforce and industry standards.
The Role of Digital Employees
The core idea behind the Optimus robots is to replace human workers on the assembly line with advanced Intelligent Agents. These robots are designed to take over repetitive tasks, increasing efficiency and cutting costs. According to Tesla, each Optimus unit could save the company up to $57,550 annually by replacing a human worker. In 2025, Tesla aims to produce 5,000 of these robots, ramping up production to 50,000 by 2026. This shift could set a new standard for cost-effective and high-efficiency manufacturing, especially for industries facing labor shortages.
Tesla's Strategy: How Robots Will Replace Human Labor
Tesla’s decision to rely on robots to perform tasks traditionally carried out by humans is part of a larger trend toward automation across various industries. The company plans to deploy Optimus in a wide range of roles within its manufacturing facilities, from assembly line work to potentially more complex tasks as the technology advances. As the global workforce continues to grapple with labor shortages, Non-Human Workers like Optimus offer a promising solution to maintain production without sacrificing quality.
Challenges and Controversies: Skepticism and Ethical Concerns
Despite the exciting potential of Optimus, there are significant concerns about the broader implications of replacing human labor with robots. Some analysts argue that the technological advancements are moving too quickly, and there are uncertainties around how effectively these robots will integrate into existing workflows. Moreover, the ethical considerations of reducing human jobs in favor of automation are raising red flags for workers and unions. Critics question whether society is ready for such a large-scale transition and whether the benefits outweigh the risks of job displacement.
The Future of Automation: What’s Next for Tesla and the Global Workforce?
As Tesla presses forward with its ambitious robot plans, the outcome of this project could have far-reaching effects on the future of manufacturing and the workforce. If successful, it could set a new precedent for how companies in other sectors adopt automation. However, the questions surrounding the viability and ethics of such a move remain unanswered. Whether or not Optimus robots will become a cornerstone of Tesla’s manufacturing process—and whether they will be widely adopted by other industries—depends on overcoming both technological and social hurdles.
A Bold Vision with Uncertain Outcomes
Tesla’s leap into robotics marks a turning point in the company’s growth trajectory. With the introduction of Optimus, Elon Musk is hoping to redefine what’s possible in manufacturing, relying on robots to enhance efficiency, reduce costs, and address labor shortages. However, the challenges of integrating such advanced technology into the workforce—along with the ethical and social implications—suggest that the road ahead may not be without bumps. Only time will tell if this ambitious vision becomes a reality, and if it does, how it will reshape industries worldwide.
Key Highlights:
- Tesla's Ambitious Plan: In April 2025, Tesla announced plans to deploy humanoid robots, known as Optimus, in its factories by the end of the year. CEO Elon Musk believes this move could increase Tesla's value to $25 trillion.
- Cost Savings and Efficiency: Each Optimus robot is expected to save Tesla up to $57,550 annually by replacing human workers in repetitive tasks, offering significant cost reductions.
- Production Goals: Tesla aims to produce 5,000 Optimus robots in 2025, with a goal of scaling up to 50,000 by 2026, marking a major shift toward automation.
- Workforce Impact: The deployment of Digital Employees in the manufacturing process reflects a broader trend of replacing human workers with AI-driven robots to address labor shortages and improve efficiency.
- Challenges and Concerns: While promising, the plan has sparked skepticism from analysts and concerns about the ethical implications of job displacement. The feasibility of fully integrating robots into the workforce remains uncertain.
- Industry Implications: The success or failure of Tesla's robot initiative could influence the broader adoption of robotics in manufacturing and set a precedent for other industries considering similar automation efforts.
Reference:
https://www.cnbc.com/2025/04/16/why-teslas-turn-to-robots-has-divided-wall-street.html