Rise of the Digital Workforce: How Humanoid Robots Are Reshaping Warehouses in 2025
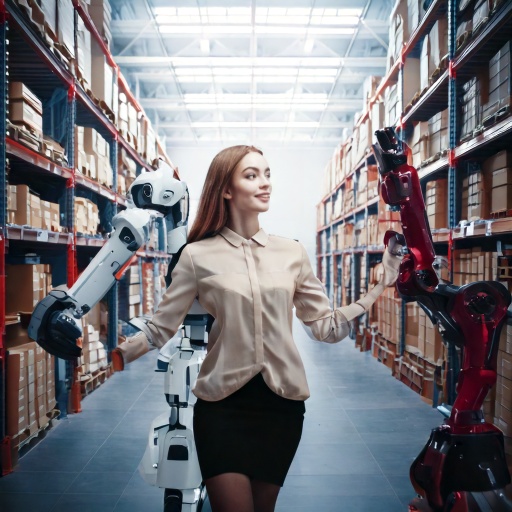
Billions Flow Into the Age of Digital Employees
In April 2025, a technological shift is sweeping through warehouses and manufacturing floors as humanoid robots—or as many are now calling them, Digital Employees—begin to play key roles in physical labor tasks. These Intelligent Agents are no longer just experimental machines—they’re becoming a vital part of logistics strategies for some of the world’s biggest companies.
Backed by a surge of investment, the humanoid robotics sector is expected to attract $3 billion in venture capital this year alone. This surge marks a significant increase in confidence among investors and tech firms betting on the future of Non-Human Workers in physically demanding industries.
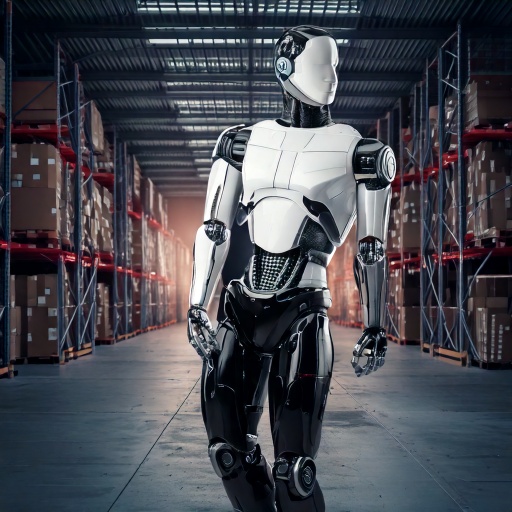
Tech Giants Lead the Charge
Major corporations are already piloting humanoid robots across their operations. Amazon, BMW, and Ford are among the companies integrating robots to improve efficiency, reduce costs, and handle tasks that are difficult to automate using traditional machines.
One standout example is GXO Logistics, which is testing robots developed by Agility Robotics and Apptronik. These Digital Employees are performing tasks like moving heavy totes, recycling materials, and navigating warehouse environments alongside human staff.
Smarter, Faster, and Easier to Train
The recent leap in AI, robotics, and natural language processing has made these humanoid robots smarter and more adaptable. Unlike rigid automation systems, they are designed to function in environments created for humans. This flexibility makes them ideal for tasks where dexterity and situational awareness are required.
Humanoid robots like Digit (by Agility) and Apollo (by Apptronik) are not just lifting boxes—they are using sensors, cameras, and onboard intelligence to work safely and effectively alongside human coworkers.
Challenges on the Road to Adoption
Despite the hype, challenges remain. Experts point out that the humanoid shape may not always be the most efficient design. Some tasks might still be better handled by robotic arms, conveyor belts, or even software-only solutions. In addition, the cost and durability of these machines need to improve before they can be deployed at scale.
Nevertheless, the push toward automation is driven by real needs—such as labor shortages, rising operational costs, and the demand for 24/7 efficiency. As companies navigate these realities, Non-Human Workers are likely to play a growing role in the future of logistics and manufacturing.
Why It Matters
The adoption of humanoid robots isn't just about shiny new gadgets—it’s about redefining how work gets done. As we enter an era where Digital Employees become the norm in warehouses, the entire concept of labor, workforce dynamics, and productivity is being reimagined.
Key Highlights:
- $3 Billion in Funding
Venture capital investment in humanoid robotics is expected to hit $3B in 2025—signaling major confidence in the future of Digital Employees. - Big Names on Board
Companies like Amazon, BMW, Ford, and GXO Logistics are piloting humanoid robots to tackle warehouse tasks. - Intelligent Agents at Work
Robots such as Digit (Agility Robotics) and Apollo (Apptronik) are now lifting, moving, and recycling in live warehouse environments. - Smarter Technology
Advances in AI and natural language processing allow these robots to adapt, learn, and function in human-designed spaces with minimal training. - Real-World Use Cases
GXO uses robots for moving totes, recycling, and even working alongside humans, aiming to increase warehouse productivity. - Challenges Remain
Concerns include high costs, durability, and whether the humanoid form is always the best design for efficiency. - April 2025 Relevance
The shift is happening now, addressing urgent labor shortages and redefining the future of work in logistics.
Reference:
https://www.businessinsider.com/humanoid-robots-reshape-warehouses-tech-invests-billions-2025-4